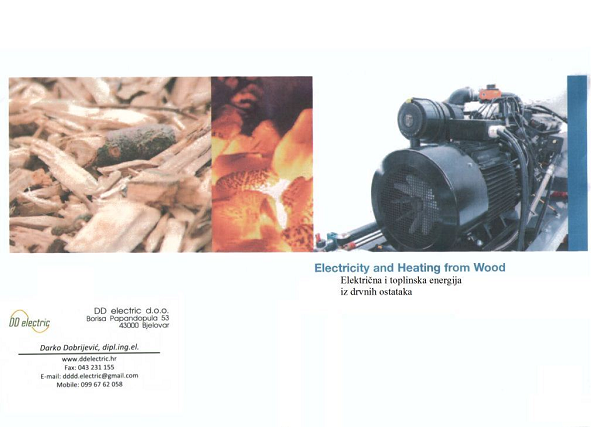
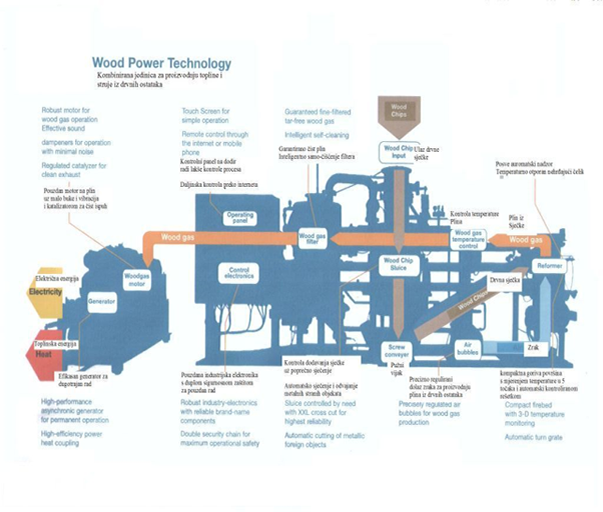
The wood gasification
Technologies of wood gasification (pyrolysis) are less present in the world, and are more efficient than the known classical technologies for the production of heat and electricity from wood residues.
Classical technology for obtaining heat and power is based on burning wood for heat and using turbines to produce electricity.
Wood is too valuable to be burned!
The gasification principle for production of heat and electricity used in a cogeneration plant (wood-cogeneration plant) uses wood optimally and to conserve natural resources!
The heart of a cogeneration system is efficient, robust thermal and electrical system that uses wood chips for the production of wood gas in the reformer.
The gas engine uses wood gas for driving asynchronous generator that produces electricity.
The efficiency of the system is seen in the consumption of 1Kg wood chips for production of 1KW of electricity, which means that for a cubic meter of wood chips the machine produces 1,000 KWh of electricity.
The thermal energy that is produced is three times greater than the produced electric energy and can be used to heat buildings, the heat emission in the heating network, ..
If we observe the system that produces 45 KW of electricity and 120 kW of thermal energy, and consumes 270 tons of wood chips for 6000 hours of operation then you can see that the system is very efficient.
We should take into account that the production of wood-gas is almost independent of the quality of wood (bark, branches, ... are used for wood chips), which significantly reduces costs in the production of heat and electric. energy.
System maintenance is simple and can be done without the need for expert, but it should provide 20 minutes a day for basic maintenance.
The production of gas (wood gas) is a thermochemical process of generating gas from wood chips. It has been known process, but the technology has become more reliable and accessible recantly.
The gas produced is filtered and used as fuel in a gas engine that powers a generator.
The produced electricity is transmitted to the network, and the heat is used for space heating, drying, ...
Wood chips are delivered using an filling screw from the storage chips in the charging unit chips (filling).
The filling unit consists of two flaps connected by air cylinders and controlled by the PLC in a way that both flaps are not open at the same time.
In the event of failure of all the valves are closed.
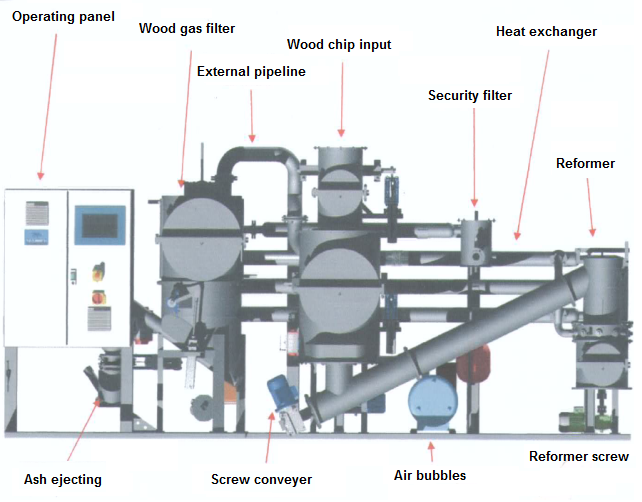
The wood is transported to the reformer by the reformer screw, and the level sensor in the reformer controls wood intake.
The reformer is a heart system, and the thermochemical reaction , process in which wood gas is formed occurs in it .
The lower the fuel (wood) drops in the combustion zone (oxidation) the temperature increases.
At a temperature of 200 to 500 °C the pyrolysis begins, the decomposition of the wood starts and gas production begins.
After pyrolysis zone (pyrolysis) the fuel is converted into carbon, and goes in the oxidation zone.
Here are some of the carbon is burned with the addition of air at the temperature of about 1200 ° C. The air supply takes place via a pressure blower, so the air is added to the reformer.
In the DC gasifier is the fire bed of the oxidation zone in the constricted area of the reformer.
Carbon dioxide is formed during combustion, and it is converted by the absorption of moisture from the steam into carbon monoxide and hydrogen in the reduction zone.
The gases pass through the firebed (oxidation zone), problematic tar and hydrocarbon gas are split to a large extent in CO, CO2 and H2.
This process produces gas with low tar content, (almost tar free).
Thermochemical reactions:
The zone of oxidation (oxidation zone)
C + O2 - CO2
C +1 / 2O2 - CO
H2 +1 / 2O2 - H2O
The zone of separation (reduction zone):
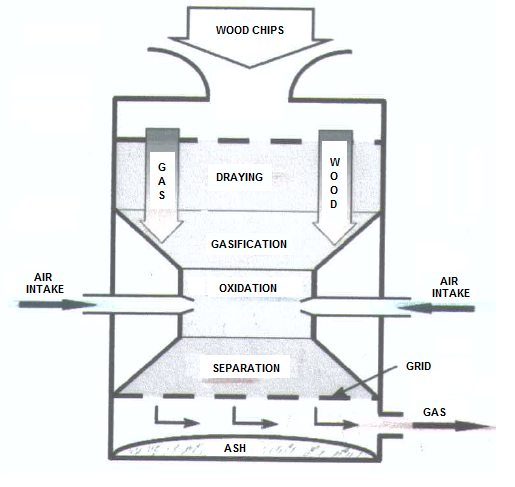
C + CO2 - 2CO (equilibrium)
C + H 2 O - CO + H2 (water-gas reaction)
C + 2H2 - CH4 (methane reaction)
Gas (wood gas) leaves the reformer at the bottom at a temperature of 800 ° C.
Ash and residue coal particles together with the gas passing through the heat exchanger where the gas is cooled to a temperature of 130 ° C. After that, the gas passes through a filter which separates ash and coal particles.
The charcoal and ash are discharged in a metal container.
After gas (wood gas) leaves the filter, it is cooled to 90 ° C in the heat exchanger so that the gas can pass through the safety filter (emergency filter).
The safety filter (emergency filter) protects the motor in case that the dust is present in the gas (wood gas) due to insufficient treatment of the main filter.
The gas is then mixed with the air and supplied to the gas engine at a temperature of about 40 °.
Lower calorific value gas is 4.5MJ / m3 (1.4KWh / m3)
Engine exhaust gases are discharged outside through an catalytic converter and an exhaust gas heat exchanger via an exhaust pipe.
All of the above is carried out in unit components that are tightly connected to one another . Everything is kept with a pressure air blower to up to 100 mbar.
The process air enters the reformer in the closed system.
The gas output from reformer also conducted through a closed system and can lead to a gas engine where the gas is burned.
In case of any defect the unit switches off, and all the flaps close. A flaring of excess gas is not necessary.
The heat obtained in the different process steps is taken up by two water- filled thermal systems.
In the gas cycle, the water is passed through the gas / water heat exchanger , and then to the filter.
The system is connected to a water circuit of the customer through a plate heat exchanger in order to give off the heat from the cogeneration system to the consumer.
Electricity is transmitted to the power grid or used for own consumption.
The use of renewable energy has a positive impact on the environment in terms of reducing local pollution and global warming, increases local employment and increase security of electricity supply. This is why most European countries introduced incentives to use renewable energy sources including Croatia, whose level of termination of profitability is estimated at 317 MW or 5.5% of total electricity production.
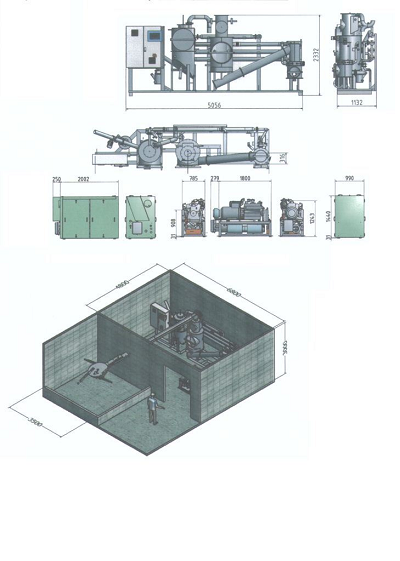
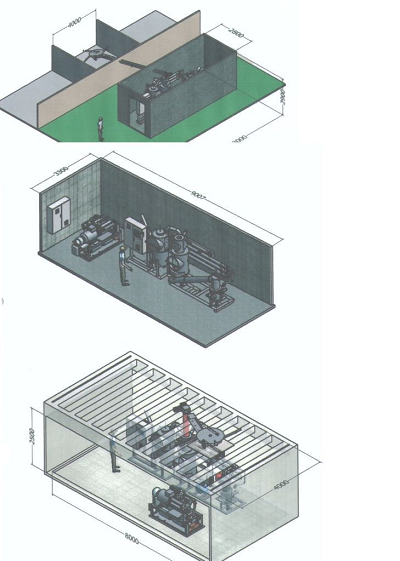